PI piezo drivers and motion controllers offer:
- High linearity, high long-term stability
- Positioning with subnanometer accuracy
- Noise approx. 1 mV (RMS value)
- Low power consumption
- Notch filter for higher bandwidth
- Output voltages adapted to various piezo actuators and piezo drives
- Analog interfaces for fast direct commanding in real time
- Short circuit protection
Low-Noise and Drift-Free Piezo Amplifiers
The characteristic properties of piezo actuators include the generation of large forces and fast response. In electrical terms a piezo element corresponds to a capacitance. A rapid change to the operating voltage brings about a rapid displacement of the actuator and thus a change in position. When the control voltage suddenly increases, the piezo actuator can achieve its nominal displacement in only a few microseconds. A prerequisite for this is that the power supply provides sufficient current to charge the capacitance. For steady state operation, i.e., when holding a certain position, the stability of the power supply is crucial, as the piezoelectric actuators already respond with motion to the slightest voltage changes. Noise or drifting must therefore be avoided as far as possible.
Applications with high load cycles exist, for example, in materials processing or in mechanical engineering during tool adjustment in milling and cutting machines. The actuators employed here operate with high forces and high dynamics and generally have a high electrical capacitance. As regards actuator control, the energy consumption of the amplifier is important. PI offers switching amplifier electronics, with which the pulse width of the control signal is modulated (PWM) and the piezo voltage is thereby controlled. This results in an especially high efficiency. In addition, a patented circuitry for energy recovery is integrated: When the piezo actuator is discharged, part of the returning energy is stored in a capacitive store and is made available again for the next charging operation. This permits energy savings of up to 80 % to be realized.
Unlike conventional class D switching amplifiers, PI switching amplifiers for piezo elements are current- and voltage-controlled. This patented system also makes them suitable for applications in active vibration damping. Here, adaptation to the currently required dynamic range is important.
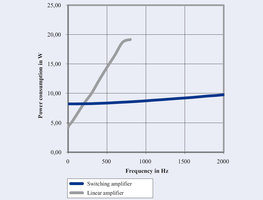
Application Examples
Charge control is based on the principle that the displacement of piezo actuators is much more linear when an electrical charge is applied instead of a voltage. In the first case, hysteresis is only approximately two percent compared with between 10 to 15 percent when using voltage control.
Therefore, charge control can often be used to achieve the required precision even without a servo loop. This enhances the dynamics and reduces the costs. Charge control is not only of advantage in highly dynamic applications but also when it comes to operation at very low frequencies.
As the drift in position of the piezo actuator is not adjusted, charge control does not replace position-controlled operation for tasks where positions need to be maintained for longer periods.
Application Examples
Closed-loop position control compares the target position with the position measured by the sensor (actual value) and automatically compensates for the nonlinear properties of the piezo actuator, such as hysteresis and drift.
Position control is based on a proportional integral control loop specifically optimized for piezo operation. One or more adjustable notch filters considerably improve usable bandwidth and dynamics because fringe effects due to system-intrinsic resonances are suppressed before they can affect the system stability.
Optimized control algorithms minimize settling times so that the closed-loop piezo positioning systems from PI can achieve a repeatability down to the subnanometer range and bandwidths to 10 kHz.
Controller Tuning / Calibration
To optimize system performance, various information about the application is required, such as the desired operating frequency, the size and weight of the payload, or the spring constant of a preload in relation to which the piezo actuator is operated.